
Original motor designs (manufactured from 1950 to 1980) allow for modifications that can make repairs to your existing electric motor a better choice than buying a replacement. HECO has performed hundreds of successful redesigns for improved and longer lasting motor windings. Our all-in-one process VPI penetrates and coats the windings completely with 4 to 5 ml build. Extensive studies have shown epoxy resins (such as HECO’s Von Roll Permafil® 74035 & HECO’s Von Roll Permafil® 74050T high voltage resin) to have superior chemical resistance, sealing/bonding, and heat-transfer characteristics. Vacuum Pressure Impregnation (VPI) with Solventless Epoxy Resin is used for sealing and bonding insulation materials.Detailed electrical tests are performed based on IEEE Standards to confirm winding integrity throughout the winding process.Compatibility of all insulation materials is confirmed for a congruent and consistent system with improved longevity and insulation life.All insulation materials used are included in this detail to provide the correct slot fit of all form coils. The coil design is then CAD drawn for detailed dimensional fit to the slot.

(“Class H” insulation materials and inverter-duty wire insulation are standards.) Design details such as volts/turn are evaluated with every rewind for improved turn-to-turn insulation protection. The original insulation system is evaluated, and a new insulation system is developed for improved dielectric integrity and heat transfer.In some cases, an improved design is proposed. The original winding data is then confirmed using engineering computer programs to calculate winding design parameters and to verify the winding is correct as is.Collected data is documented on detailed winding data forms and through accompanying digital images.
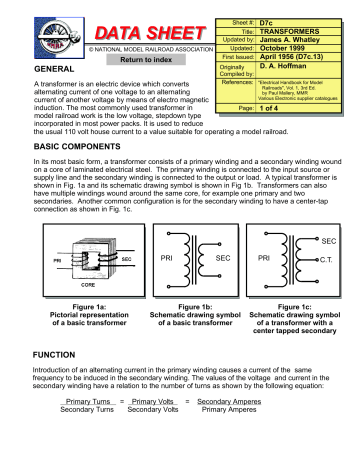
